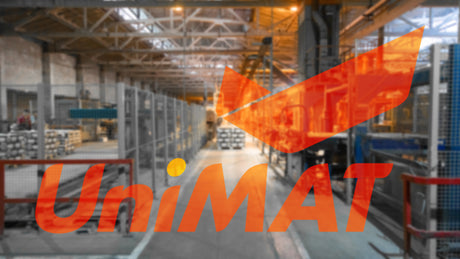
Успешная интеграция UniMAT в отрасль строительных материалов: пример
Автор UniMAT
Введение: Строительная промышленность полагается на передовые решения по автоматизации для оптимизации производственных процессов и удовлетворения растущего спроса на качественные строительные материалы. В этом примере рассматривается успешное сотрудничество между UniMAT, вымышленной...