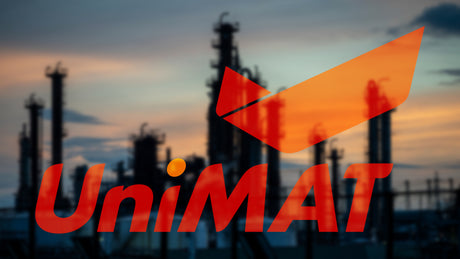
UniMAT's Automation Excellence in the Petrochemical Industry: A Case Study
By UniMAT
The petrochemical industry is a vital sector that demands seamless automation solutions to enhance productivity and ensure safety. In this case study, we explore the successful collaboration between UniMAT, an...