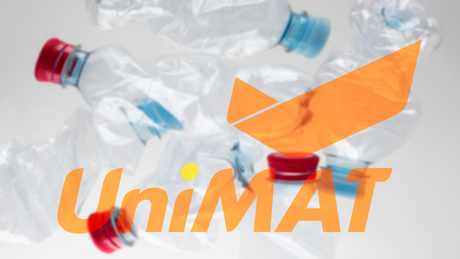
Application of UniMAT PLC in Control System of Plastic Recycling Granulator
By UniMAT
The research institute develops and produces 16-zone single-screw plastic recycling granulator for customers. Its control unit includes host heating system, host speed regulation system, traction control system, cutting control system...