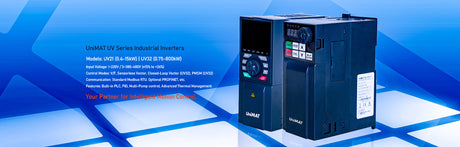
What is a Frequency Inverter? A Complete Guide to How It Works & Benefits
By UniMAT
What is a Frequency Inverter?A Complete Guide If you've ever worked with industrial machinery,HVAC systems,or even some high-end appliances,you've likely heard the term"frequency inverter."But what exactly is it,and why is...