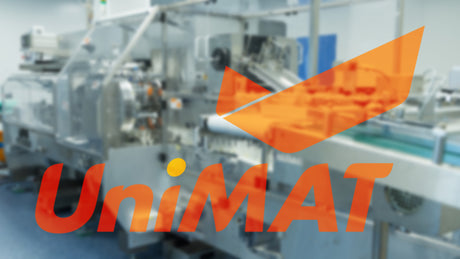
UniMAT's Successful Integration in the Packaging Machinery Industry: A Case Study
By UniMAT
The packaging machinery industry relies on advanced automation solutions to optimize production processes, ensure product quality, and meet the demands of diverse packaging requirements. This case study highlights the successful...